LNG (Liquefied Natural Gas) Fuel Will Be Transported by Electric Ships
The British Emerald was the world’s largest LNG carrier when it launched in 2007. It was also the first vessel built by Hyundai Heavy Industries that used GE’s electrical propulsion technology. The ship generates electricity by burning waste gasses that evaporate from the holding tanks. The power generators can also switch to diesel. (Credit: General Electric)
New natural gas production methods (like hydraulic fracturing) had already had a major positive impact on the economy of gas-rich countries like the U.S. and had even led to a visible decline in energy-related carbon emissions. These benefits will soon reach many distant shores as shipyards in Korea and in other countries are building new liquefied natural gas (LNG) carriers to move the fuel around. Many of the new supertankers will use electric propulsion systems.
Two of the world’s largest shipyards, Hyundai Heavy Industries and Daewoo Shipbuilding & Marine Engineering, are working on new massive carriers powered by heavy-duty GE motors, generators, transformers and other technology. GE Power Conversion has signed contracts to supply propulsion systems for an armada of 31 LNG vessels over the last year.
Electric ship propulsion has been around for a century. Although it has been long considered an inefficient novelty, engineers perfected it in the last few decades. “We started the marine electric propulsion story,” says Jean-Philippe Chaignot, a marine propulsion leader at GE Power Conversion.
Electric motors designed by GE engineers now power some of the biggest and most sophisticated vessels, from aircraft carriers and destroyers to tankers, cruise ships and Queen Mary 2, the largest ocean liner ever built and the fastest one in service.
The ships use either diesel or gas to produce electricity. The new electric propulsion design leaves more open space for cargo because the generator and the propeller do not need to be connected by a rigid shaft anymore. Instead, the new design allows ship operators transfer power from the electricity generator to the propeller motor by a flexible cable. The electric system also cuts weight, noise, vibrations, and improves efficiency.
The GE propulsion systems inside the new tankers will generate enough electricity to power a small town.
There are already 30 LNG tankers powered by this GE technology, 70 cruise ships, and dozens of other merchant and military vessels. Just this month the company announced that it signed a $14 million contract to fit the USS Mount Whitney command ship with new electric gear.
Popular Mechanics wrote in 1920 that “as to the operation of electrically driven vessels, the bugaboo as regards electricity is fast leaving the minds of the ship owners, who are coming to realize that, instead of introducing difficulties in the matter of operating force, the adoption of the electric drive will eliminate them and make ships considerably less dependent upon the skill and resourcefulness of crews.” Alas, that claim has come to pass.
GE’s Propulsion Systems for 23 New LNG Ships
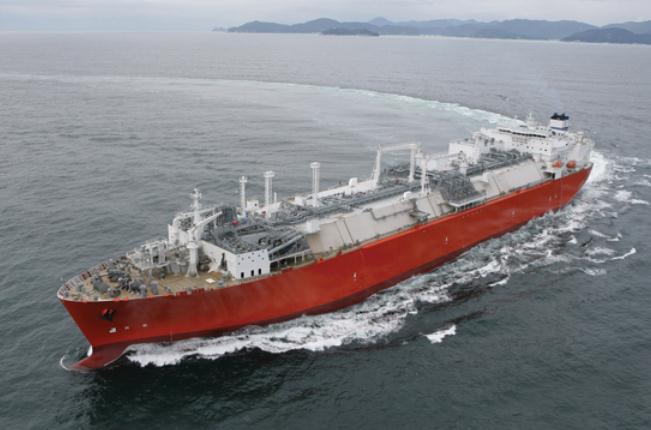
1 of 23 LNG hybrid-electric ships
The scope of GE’s contracts includes MV7000 converters, induction motors, transformers, generators, main and cargo switchboards and propulsion control systems. Manufacturing for all propulsion motors is based in GE’s rotating machines plant in Nancy, France, while the propulsion systems are engineered at the GE merchant marine center of excellence in Belfort, France.
GE’s motors and converter are designed and optimized to make the propulsion systems easy to maintain. The induction machines are driven by press-pack IGBT Pulse Wide Modulation (PWM) converters to offer high levels of reliability in a compact design. GE’s global electric propulsion systems provide customers with high efficiency, availability and layout flexibility.
GE’s Growing Role in the LNG Ship Propulsion Sector
Traditionally, the propulsion of LNG tankers has been based on boil-off boilers and steam turbines. In recent years, more and more ship owners have turned to dual-fuel engine systems combined with electric propulsion as more efficient solutions, up to 30 percent at high loads. Moreover, these solutions increase cargo capacity by 3 to 5 percent as they enable the ship designer to optimize the equipment layout.
GE’s Power Conversion unit was the first company to equip a full-size LNG carrier with electric propulsion. The order was placed in 2002 for the vessel Gaz de France Energy. This milestone project was followed by a series of orders in 2005 and 2006 for eight large LNG carriers built in Korea. During the next two years, GE was selected to equip the latest generation of LNG carriers with new advanced electric propulsion systems.
Induction motors for the marine industry were developed 15 years ago by GE’s Power Conversion business for the U.S., English and French navies. Today, GE remains the only company with marine applications that combine high-powered induction motors with PWM.
Electrifying designs – to cut fuel and maintenance costs
In terms of energy efficient designs, the shipping industry has started to look seriously at ways to reduce fossil fuel consumption by building electric motors, which have been used on watercraft from submarines to research vessels.
The trend towards using renewable and alternative energy sources to fuel engines has also gained momentum over the last few years as countries look towards cutting down on pollution in the maritime sector.
Here, we compare the latest generation of ship engine designs that are expected blow the last generation of machines out of the water.
GE Power Conversion’s Captain Mark Dannatt, a retired Royal Navy captain, recently said: “I’ve seen the future of naval propulsion, and it’s electrifying.”
Speaking at the Euronaval exhibition and conference in Paris in October, he explained that maritime operations require ships which are operationally dependable, financially efficient and respect the environment.
Under these circumstances, electrical propulsion is worthy of further investigation based not only on fuel and maintenance costs but also on the consequential impact on improvements in ship availability, Dannat said.
GE’s Power Conversion business is currently supplying its electrical propulsion drive train for the UK Royal Fleet Auxiliary’s (RFA) new fleet of Military Afloat Reach and Sustainability (MARS) tankers.
The RFA is replacing its existing, single-hulled tankers to meet International Maritime Organization pollution regulations, as well as stringent European Commission environmental regulations.
In a draft legislation approved in September 2012, the commission states that under a business-as-usual scenario, the emissions of the maritime sector will surpass emissions from all land-based sources, reinforcing the need for greener propulsion systems.
But it’s not just the navy that’s benefiting from electrified propulsion; Norway’s Sustainable Electric Propulsion Systems (STADT) has designed a hybrid electric converter for use in seismic research vessels, including Det Norske Veritas’s MS “Sanco Spirit” and various other ships.
The Stascho electric propulsion system is available in models from 100kW to 100MW and supplies sinusoidal voltage and current to the electric motor and back to the main switchboard. This ensures that there is no interference from inverter drives on other sensitive electronic equipment on the ships.
While STADT has designed a system that integrated AC electric motors, General Atomics (GA) is developing a 36.5MW superconducting DC homopolar motor for ship propulsion.
The company argues that motors using DC power are significantly quieter, smaller – due to fewer components – and more efficient than AC motor systems, and are suited to simpler, less costly ship electrical distribution architectures.